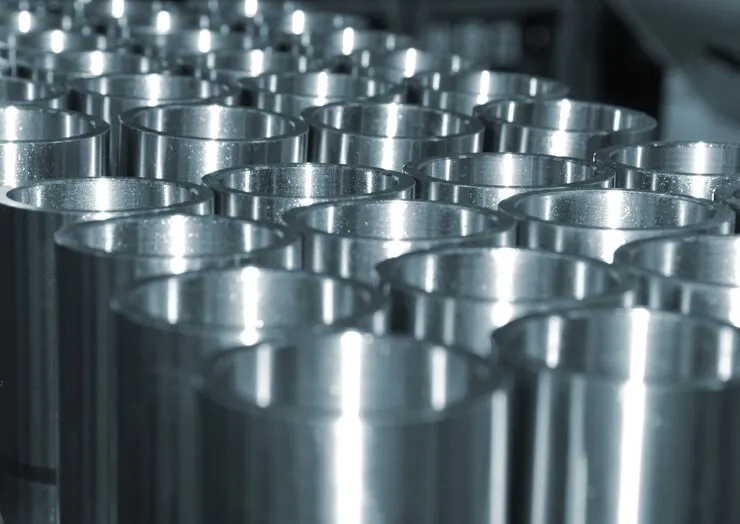
About
stainless steel
Stainless steel jewelry is typically made from two grades of stainless steel: grade 304 and grade 316.
304 stainless steel, also known as 18-8 stainless steel, boasts 18-20% chromium and 8-10.5% nickel, ensuring remarkable corrosion resistance. Perfect for crafting exquisite pieces, its non-magnetic properties and lustrous finish make it a favorite among jewelry artisans.
For enhanced durability and performance, consider our 316 stainless steel jewelry. With the addition of molybdenum, it surpasses 304 in corrosion resistance, heat tolerance, and overall longevity. Trusted by renowned brands worldwide, our 316L grade stainless steel pieces promise enduring beauty and quality craftsmanship.
Although both stainless steels are in compliance with European Union REACH and California Proposition 65, most renowned brands opt for 316L grade stainless steel. Some manufacturers choose 304 grade because it’s cheap .
About Stainless Steel processing technology
cutting-edge technology
In the process of crafting stainless steel jewelry, laser cutting plays a pivotal role. At Haosen, our cutting-edge technology harnesses a potent laser beam ranging from 1,000 to 4,000 watts, adept at slicing through stainless steel plates spanning 0.4 to 10 millimeters in thickness. This precision enables the creation of bespoke components with intricate designs.
Various stainless steel grades like 304 and 316L can be seamlessly cut using our state-of-the-art laser cutters. The efficiency of cutting is contingent upon the thickness of the steel, directly influencing production costs. Notably, the remnants of the cut steel plates are salvaged, melted down for recycling, thereby promoting sustainable jewelry production and cost-effectiveness.
Post-cutting, the semi-finished products undergo meticulous sanding and polishing techniques to ensure a flawless surface finish. Subsequently, these pieces are primed for additional enhancements such as plating, painting, or embellishment with dazzling diamond-encrusted jewelry for an added touch of elegance.
By leveraging laser cutting technology, the necessity for mold creation is obviated, expediting sample development processes significantly. The intricate artistry of crafting stainless steel jewelry demands specialized expertise and Haosen prides itself on possessing both cutting-edge equipment and skilled artisans to guarantee the delivery of premium-quality stainless steel jewelry products.

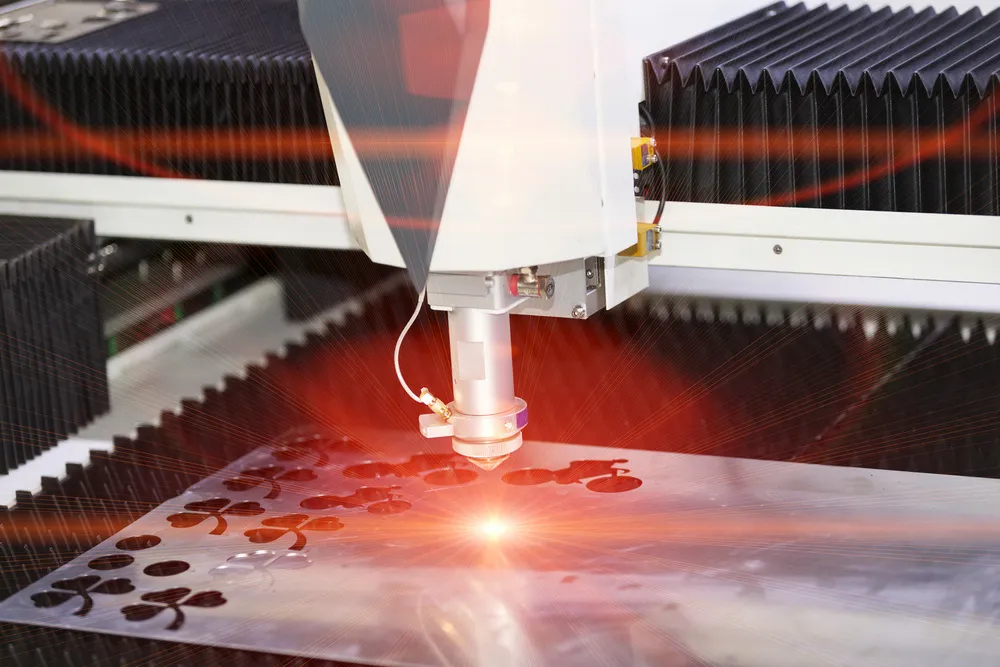
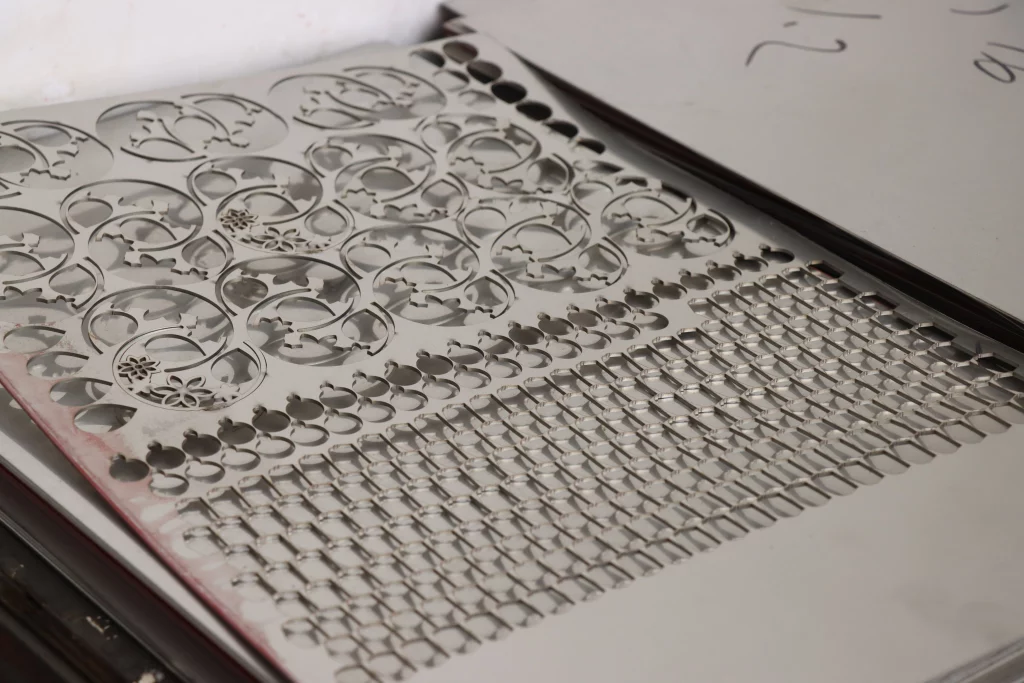

Corrosion technology
In the process of crafting stainless steel jewelry, laser cutting plays a pivotal role. At Haosen, our cutting-edge technology harnesses a potent laser beam ranging from 1,000 to 4,000 watts, adept at slicing through stainless steel plates spanning 0.4 to 10 millimeters in thickness. This precision enables the creation of bespoke components with intricate designs.
Various stainless steel grades like 304 and 316L can be seamlessly cut using our state-of-the-art laser cutters. The efficiency of cutting is contingent upon the thickness of the steel, directly influencing production costs. Notably, the remnants of the cut steel plates are salvaged, melted down for recycling, thereby promoting sustainable jewelry production and cost-effectiveness.
Post-cutting, the semi-finished products undergo meticulous sanding and polishing techniques to ensure a flawless surface finish. Subsequently, these pieces are primed for additional enhancements such as plating, painting, or embellishment with dazzling diamond-encrusted jewelry for an added touch of elegance.
By leveraging laser cutting technology, the necessity for mold creation is obviated, expediting sample development processes significantly. The intricate artistry of crafting stainless steel jewelry demands specialized expertise and Haosen prides itself on possessing both cutting-edge equipment and skilled artisans to guarantee the delivery of premium-quality stainless steel jewelry products.
Casting technology
1.lost-wax Casting is a key process in the production of stainless steel jewelry. Making wax molds and silicone molds is essential preparation. During the casting process, stainless steel melted at a temperature exceeding 2000°C is injected into the wax or silicone molds and cooled to form the desired shape. Temperature control and cooling speed are crucial to prevent cracking and damage. After completion, finishing and polishing are necessary to ensure a smooth surface. The casting process can be integrated with corrosion processes, such as pre-corrosion before casting assembly or casting first followed by corrosion for embellishment, adding layers and details.
2.Powder metallurgy castingPowder metallurgy is a metal forming process, in the process of stainless steel jewelry production, the selection of suitable stainless steel metal powder as raw materials, through pressing and sintering and other processes, the metal powder is compressed into a nearly finished product process. Compared with the traditional casting process, powder metallurgy can produce very complex geometric shapes and features, powder metallurgy process in the production process can greatly reduce the subsequent production process, thereby reducing production costs and improving production efficiency.
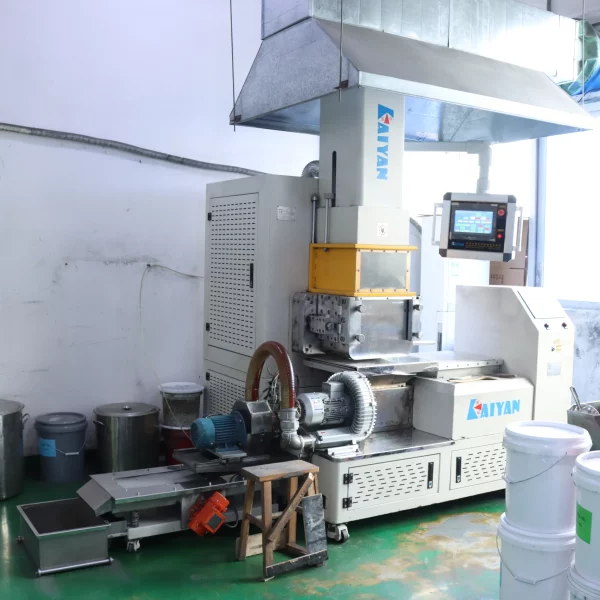

Hydraulic Press technology
Stainless steel jewelry production adopts the oil pressure process, by equipping with special hydraulic press and steel molds, applying 100-300 tons of pressure, it can press various shapes of jewelry, which is more capable of obtaining fine effects compared with casting.
After oil pressing, the jewelry needs to go through fine polishing treatment, including machine polishing and hand polishing, to show the exquisite surface effect. This process offers more possibilities for shaping stainless steel, while polishing adds sophistication to its appearance and requires skilled hands combined with the operation of equipment to ensure that the metal is transformed into a beautiful work of art.
In the hydraulic process, the creation of molds is crucial and directly determines the shape and detail of the molded product. Molds should be made of moderately hardened steel and be machined and polished to ensure smooth molding of the product. In addition, choosing the right hydraulic press is also key. You need to choose the right machine tonnage according to the product design features and pay attention to the uniformity of force application during operation.
Etching, casting and hydraulic process can be combined with other process technologies to produce richer works. For example, the combination of laser cutting and hydraulic molding, or hydraulic and etching process in conjunction with each other. This combination of processes can play to their respective strengths to create a more design-oriented work.
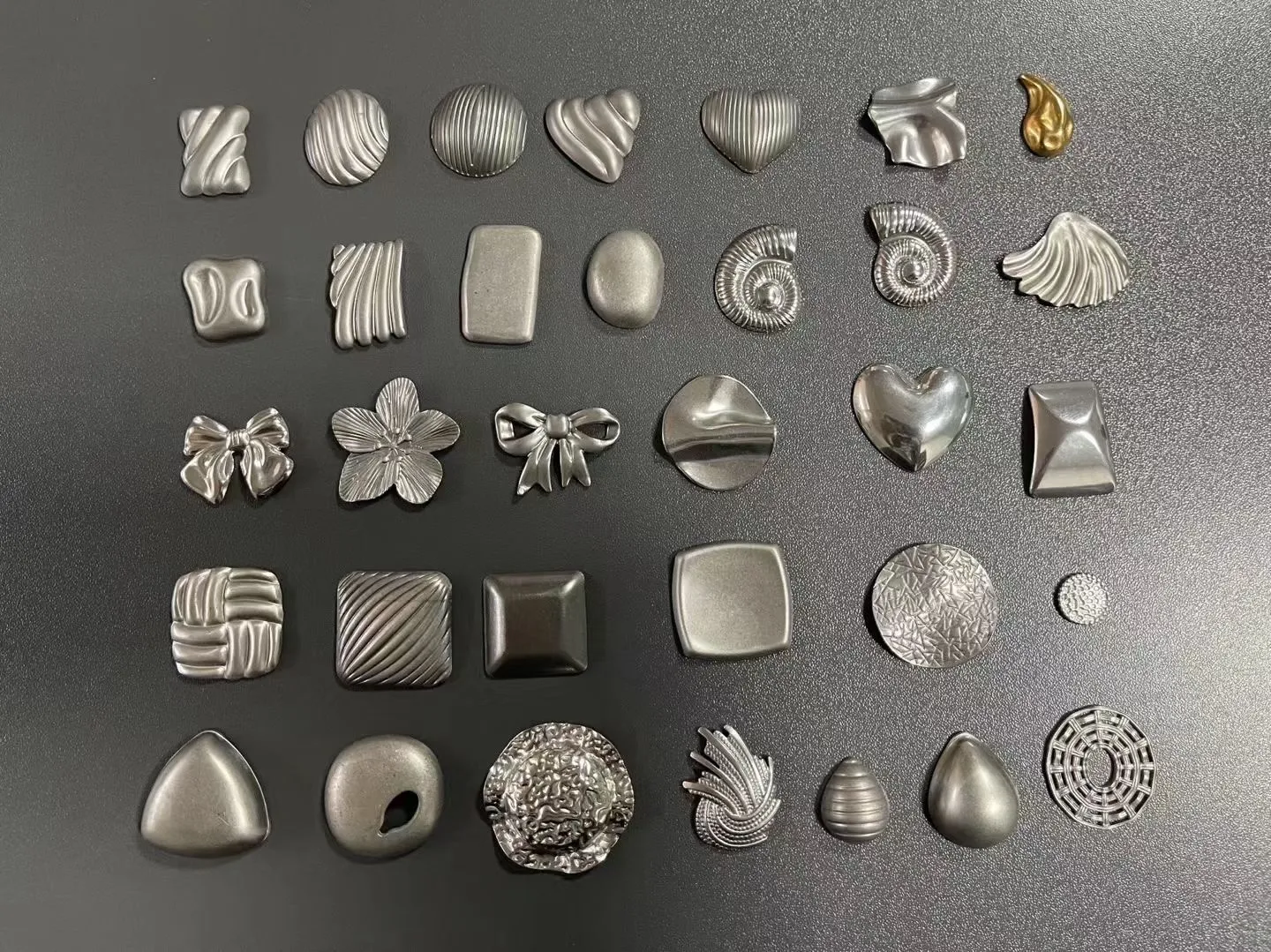
Polishing technology
Polishing is a critical step in the metal process, whereby rough and fine grinding is performed by selecting grinding wheels of varying grits to produce a substantially flat surface and improved gloss. Hand polishing uses cotton cloths or brushes to wipe the surface, apply polishing liquids or metal shiners, and rub in circular motions to achieve results that cannot be matched by machines. However, hand polishing is more demanding on the technician and requires patience and experience to achieve a fine finish. Different polishing methods can be combined with each other, for example, machine rough polishing to remove burrs and then hand polishing to increase the brightness. The technician needs to fully understand the characteristics of the various tools and skillfully combine them to achieve the best polishing results.
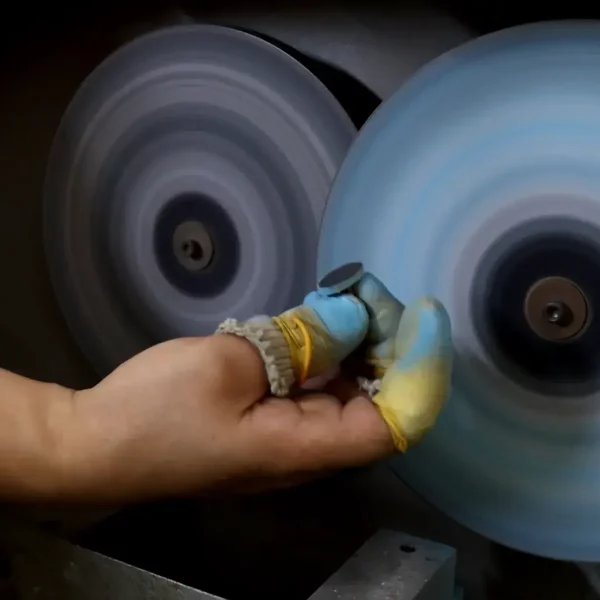
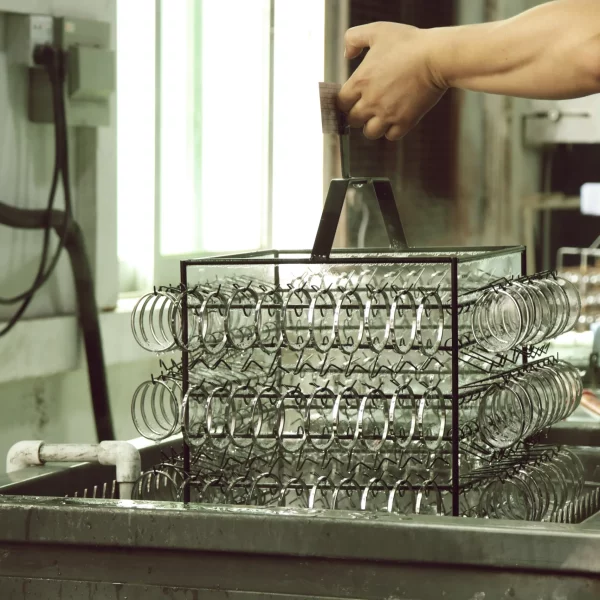
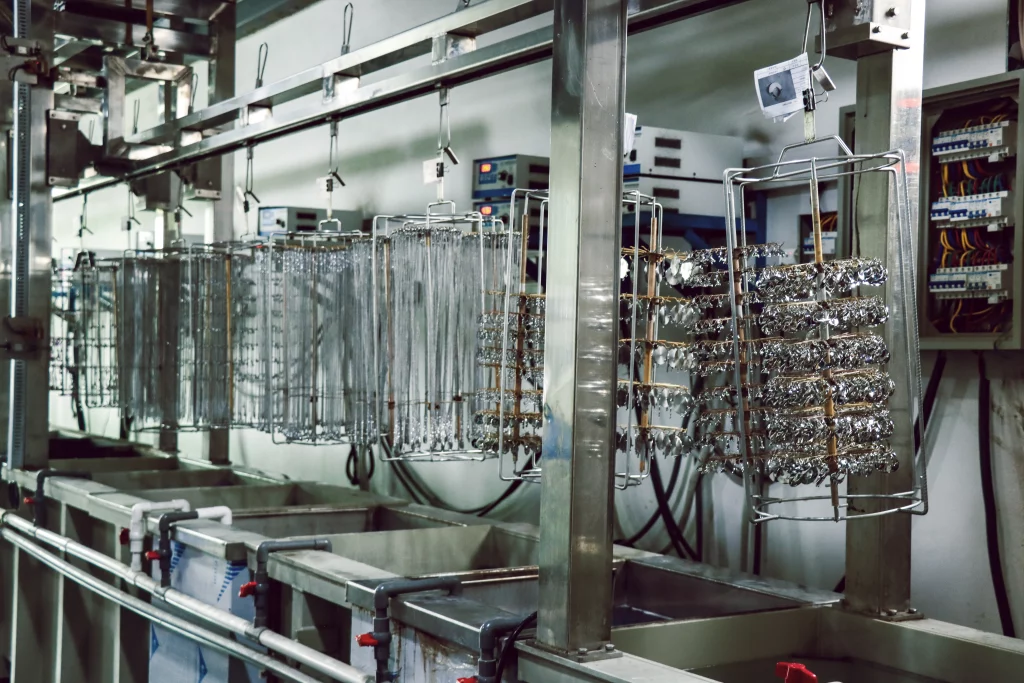
Electroplating technology
The production of stainless steel jewelry requires the use of vacuum plating technology, which ensures a long-lasting and non-allergenic metal coating compared to the traditional nickel-containing aqueous plating method. The principle is by covering the metal ions on the surface, which is different from the chemical reduction reaction of water plating. Although vacuum plating equipment is expensive and the process is complex, it creates a uniform and tightly packed coating that maintains the desired color retention.
The quality of plating is closely related to the pre-polishing process, and fine polishing results in a more delicate coating. Before plating, ultrasonic cleaning is required to remove surface impurities, and parameters such as bath concentration, current strength, and temperature are controlled during the plating process. Common plating colors are gold, platinum, etc. The steel color of stainless steel itself does not need plating.
After plating is completed, the product needs to be washed to remove pollutants and show the luster of the metal. Some of the products can also be processed with diamonds, usually using bright crystal diamonds to enhance the visual effect. Plating colors can be selected by different brands or products according to customer preference, but vacuum plating is a critical step to ensure texture and color.
Common plating colors on the market include gold, platinum, rose gold, black gold, etc. Two-tone and color plating effects are also available.
Plasma Process technology
There is also a new process called plasma process, which is a process that we have started to use in the last 3 years or so, which can penetrate more into the corners of the metal, as well as enhance the oxidation and corrosion resistance of the stainless steel itself.
Plasma technology is a kind of advanced surface treatment method that utilizes plasma to interact with the surface of stainless steel in a vacuum environment, and deposits specific materials in the form of atoms or molecules on the surface through plasma deposition or spraying to form a uniform, dense and functional coating. This technology enables customized coatings on stainless steel surfaces by precisely controlling the energy and reaction conditions of the plasma, including enhancing abrasion resistance, improving corrosion resistance, and imparting a variety of color, texture, and grain appearance effects.
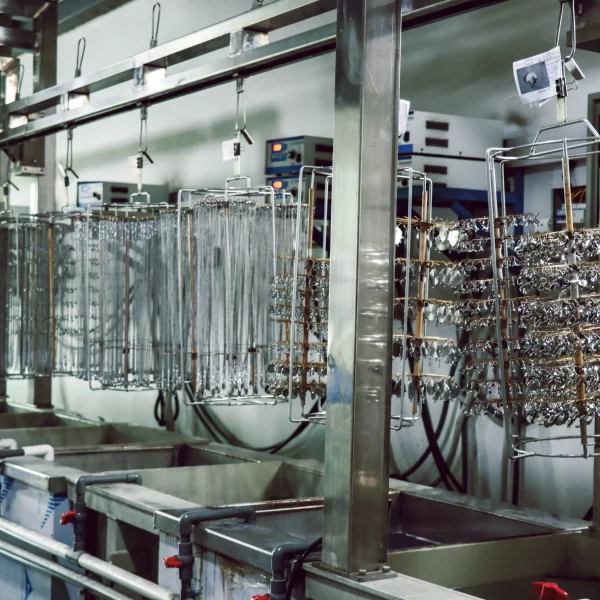